aktualisiert: 23.10.2021
9. Motor
Um einen Überblick zu erhalten und die Abstandsmaße für die Motorspante zu erhalten, baue ich die Einzelteile des Motors, des FES Ex-Uni8 Systems und die Motorhalterungen und Lagerungen zunächst einmal wie folgt zusammen:

Motor mit Zubehör
Die Motorwelle hat einen Durchmesser von 6 mm – der Innendurchmesser der FES Ex-Rasthülse beträgt 8 mm. Durch die Reduzierhülse wird hier die Differenz ausgeglichen.
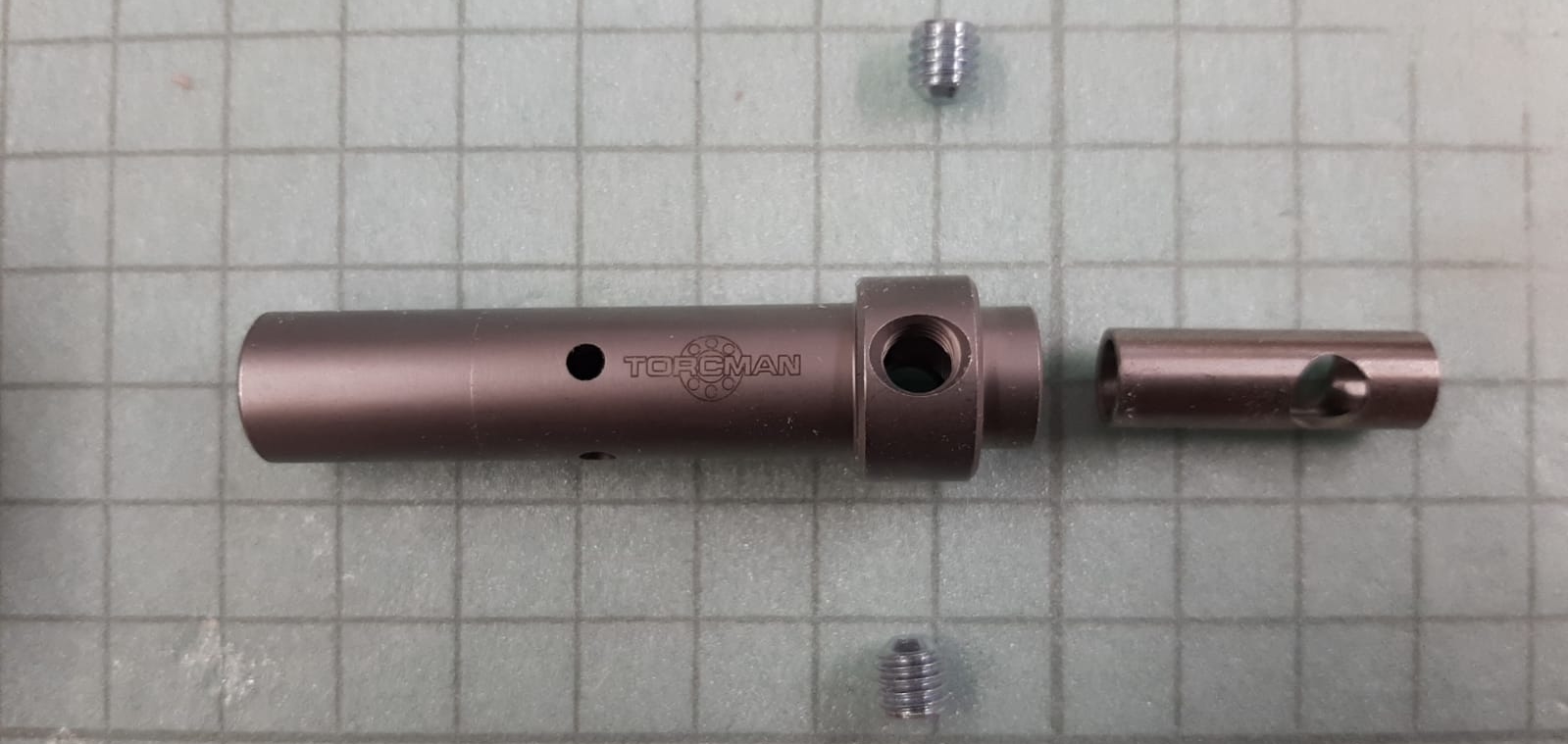
Rasthülse und Reduzierhülse für FesEx-Einheit
Die Reduzierhülse wird so eingesetzt, dass sie mit der Rasthülse bündig abschließt – die Bohrung muss mit den beiden Bohrungen der Aufnahme fluchten, damit die Gewindestifte bis zur Welle eingedreht werden können.

Reduzierhülse für FesEx-Einheit eingebaut
Damit die beiden Gewindestifte einen sicheren Halt auf der Motorwelle finden, wird diese auf beiden Seiten etwas abgeflacht.

Motorwelle beidseitig abgeflacht
Der Motorspant wird vorläufig mit den Senkkopfschrauben auf der Wellenseite am Gehäuse befestigt.
Zu einem späteren Zeitpunkt ersetze ich diesen Spant durch einen Winkel. Das war beim Erstellen dieser Fotos allerdings noch nicht geklärt.

Motorspant mit Senkkopfschrauben montiert
Die FES Ex-Rasthülse kann auf der Welle fixiert werden.

FesEx-Rasthülse montiert
Damit die Verlängerung der Welle sauber geführt ist, wird ein Lagerspant mit Flanschkugellager zur Abstützung auf die Aufnahme aufgesteckt.

Lagerspant mit Flanschkugellager montiert
Der Propmitnehmer wird eingesetzt, indem der stirnseitige Knopf eingedrückt und die Welle in die Bohrung eingeführt wird.
Sobald die federbelasteten Kugeln in den 4 Bohrungen der Rasthülse einrasten, kommt der Knopf wieder vollständig aus der Bohrung heraus.
Der grüne Ring wird sichtbar, wenn die korrekte Position erreicht ist.
Zur Sicherheit sollte überprüft werden, ob die Kugeln auch einrasten, wenn die Welle drei Mal jeweils 90° weitergedreht wird.

Propmitnehmer eingesetzt
Die Antriebseinheit:
Nach langem Planen und Verwerfen – Probieren und Umbauen – Ändern und Ergänzen ist letztendlich eine komplette Antriebseinheit entstanden, die ich im Detail nicht vollständig beschreiben kann. Meine Gedanken dazu werde ich aber gerne mitteilen:
Ich wollte eine Einheit bauen, die ich komplett einbauen und wieder entnehmen kann.
Ein Grund hierfür waren die 3 Akkus. Diese müssen zum Aufladen aus dem Modell ausgebaut werden.
Ein weiterer Grund waren die Kabel. Diese lassen sich außerhalb des Rumpfes wesentlich einfacher und sauberer verlegen, als im eingebauten Zustand.
Auch die Befestigung der einzelnen Komponenten war einfacher und sicherer zu lösen.
Die Wartung und eventuelle Korrekturen oder Reparaturen lassen sich außerhalb des Modells durchführen.
Den Bau der ganzen Einheit detailliert zu beschreiben macht aus mehreren Gründen keinen Sinn bzw. wäre auch nur möglich, wenn ich das Ganze noch einmal nachbauen und dann Schritt für Schritt fotografieren und beschreiben würde.
Zum Einen wird nicht jeder eine Motorversion bauen.
Zum Anderen wird sicherlich die Auslegung der einzelnen Komponenten unterschiedlich ausfallen.
Des weiteren stehen nicht alle Kleinteile, die ich verwendet habe, jedem zur Verfügung. Ich habe mich einfach aus meinem Fundus bedient und hier sicherlich nicht überall das ideale Material verwendet.
Und letztlich baut jeder in einem anderen Stil und mit anderem Material.
Hier zeige ich also nur eine Möglichkeit, die so vermutlich noch nicht gebaut wurde und auch kaum wieder so gebaut werden wird.
Da beim Bauen immer wieder Änderungen erforderlich wurden, sind manche Bauteile am Ende etwas anders, als auf den anfänglichen Fotos zu sehen ist.
Baubericht:
Zunächst habe ich für die Spanten 2 Winkel (50 x 50 x 35) genommen und den Kreuzspant des Motors wieder entfernt.
Zur Befestigung an der Trägerplatte wurden die Winkel mit Gewinden M6 versehen. (Kernlochbohrung 5 mm war bereits vorhanden).
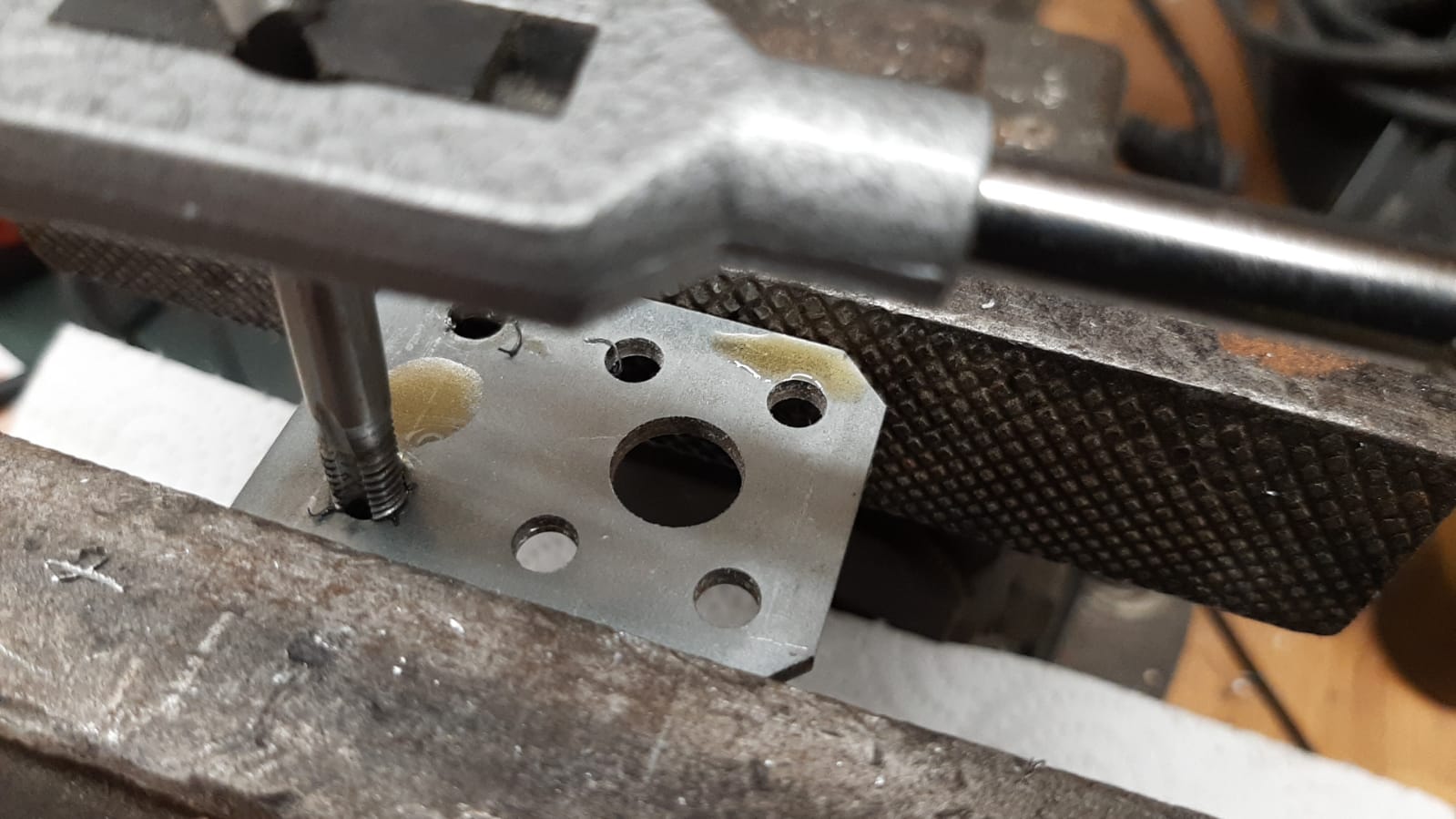
Gewinde 6 x M6
Die 11er Bohrung am stehende Flansch habe ich jeweils auf 16 mm für den Motorspant bzw. 13 mm für den Lagerspant aufgebohrt und angefast, damit die Rotorwelle sich frei drehen kann.

Bohrung am Motorspant auf 16 mmaufgebohrt
Der Lochabstand des Lagerhalterings ist zufällig der gleiche, wie der am Winkel. Somit konnte ich den Lagerhaltering einfach am Lagerspant befestigen.

Lager angeschraubt

Lager angeschraubt
Die Trägerplatte habe ich aus 6 mm dickem Sperrholz gefertigt. (sie wird später noch verändert werden)

Trägerplatte
Die beiden Winkel habe ich mit der Trägerplatte verschraubt.

Winkelmontage
Der Lochabstand der Gewinde am Motor ist ebenfalls identisch mit dem der Winkel. So war auch hier eine einfache Befestigung möglich.

Motormontage
Zur Montage der FES Ex-Einheit musste ich den Winkel noch einmal abnehmen. (wird später noch geändert).

FES Ex-Montage

Motor und Lager montiert
Um alle vier Befestigungsgewinde des Motors zu nutzen, habe ich die beiden verbleibenden Bohrungen des Winkels zu Langlöchern erweitert. Das Lochbild war hier nicht passend.

Befestigungsbohrungen erweitert
Den Motor habe ich dann um 90° gedreht um die Kabel seitlich zu positionierten.
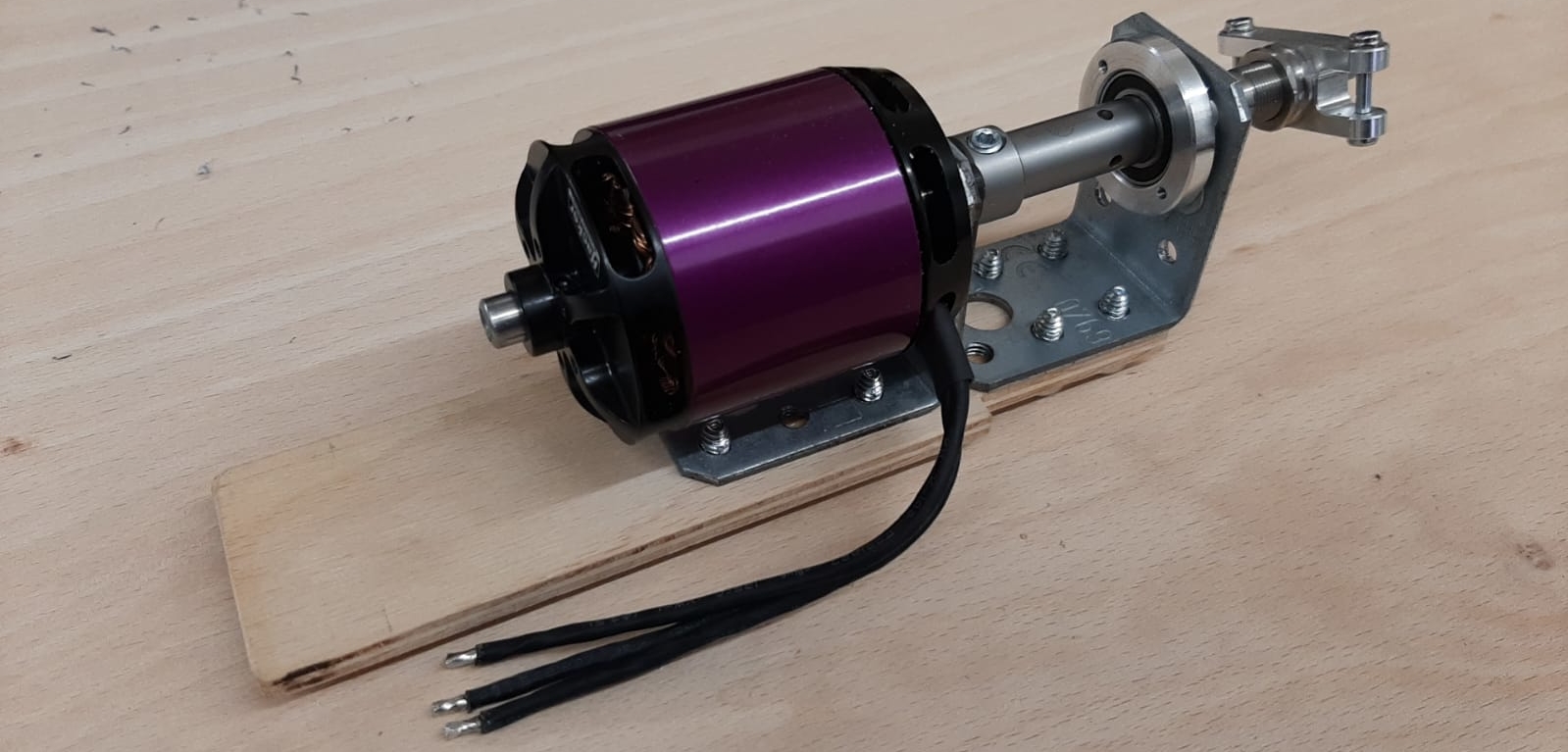
Kabelposition seitlich
Ich zeichne den Ausschnitt für die Antriebseinheit auf dem vorderen Rumpfspant an.
Die vorläufige Mitte der Rotorwelle liegt in der Mitte des Spantes.

Ausschnitt für die Antriebseinheit auf dem Rumpfspant aufgezeichnet
Die mittlere Position hätte das Entfernen oder Ausschneiden der Montageplatte im Innern des Rumpfes erfordert.
Eine aufwändige Befestigung der Antriebseinheit wäre die Folge gewesen.
Ich suchte nun eine alternative Position.
Den Motor stehend zu montieren hätte eine zu hohen Positionierung des Rotors ergeben.

Einbauvarianten
Den Motor hängend zu montieren ermöglichte die Positionierung ca. 12 mm unterhalb der Spantmitte und damit exakt in der Mitte der Nasenspitze.
Damit war eine Ideallösung gefunden.
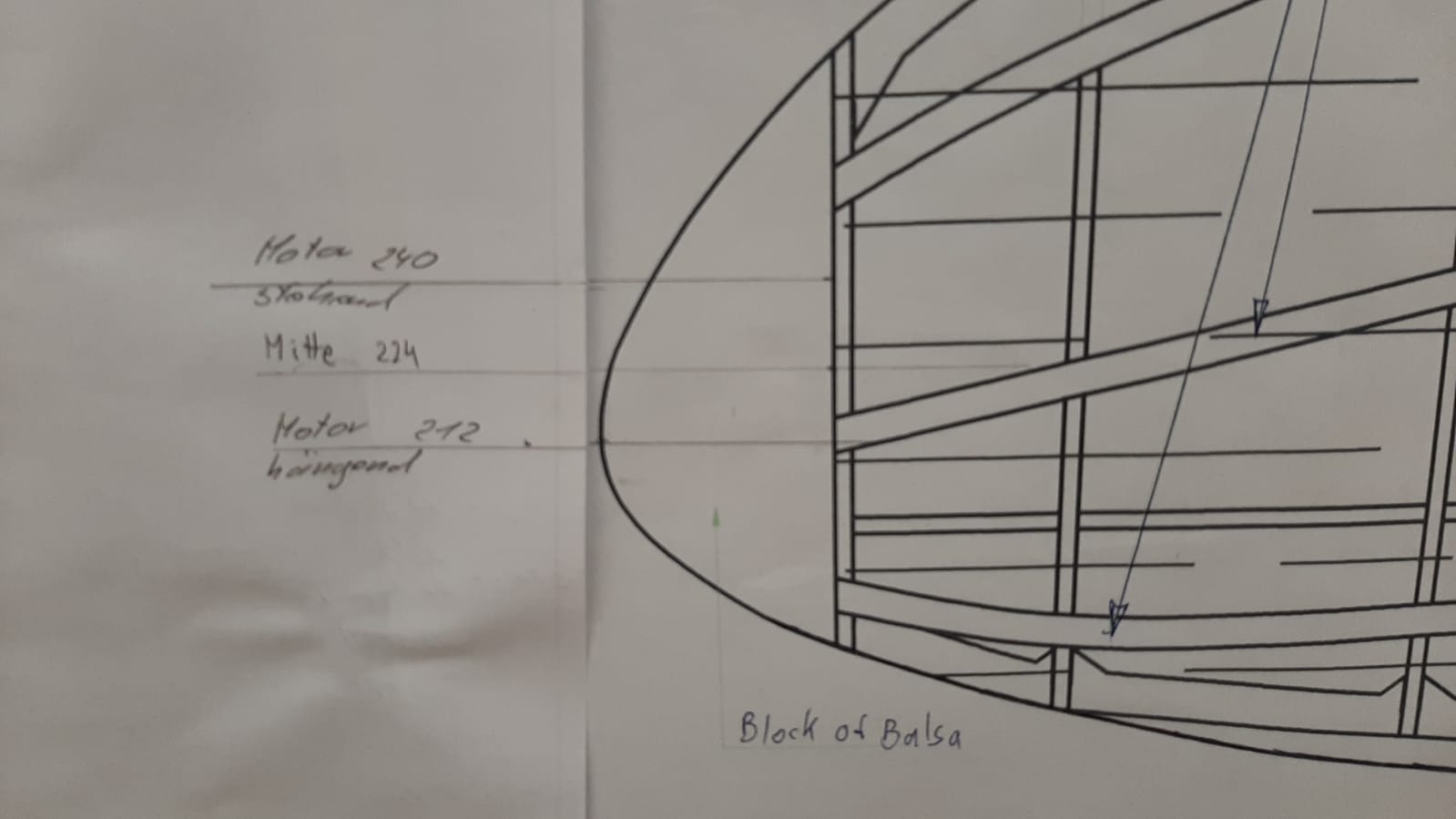
Einbauvarianten
Bei der „Anprobe“ zeigte sich, dass die Trägerplatte nicht vollständig durch die Nasenspitze verdeckt werden konnte.
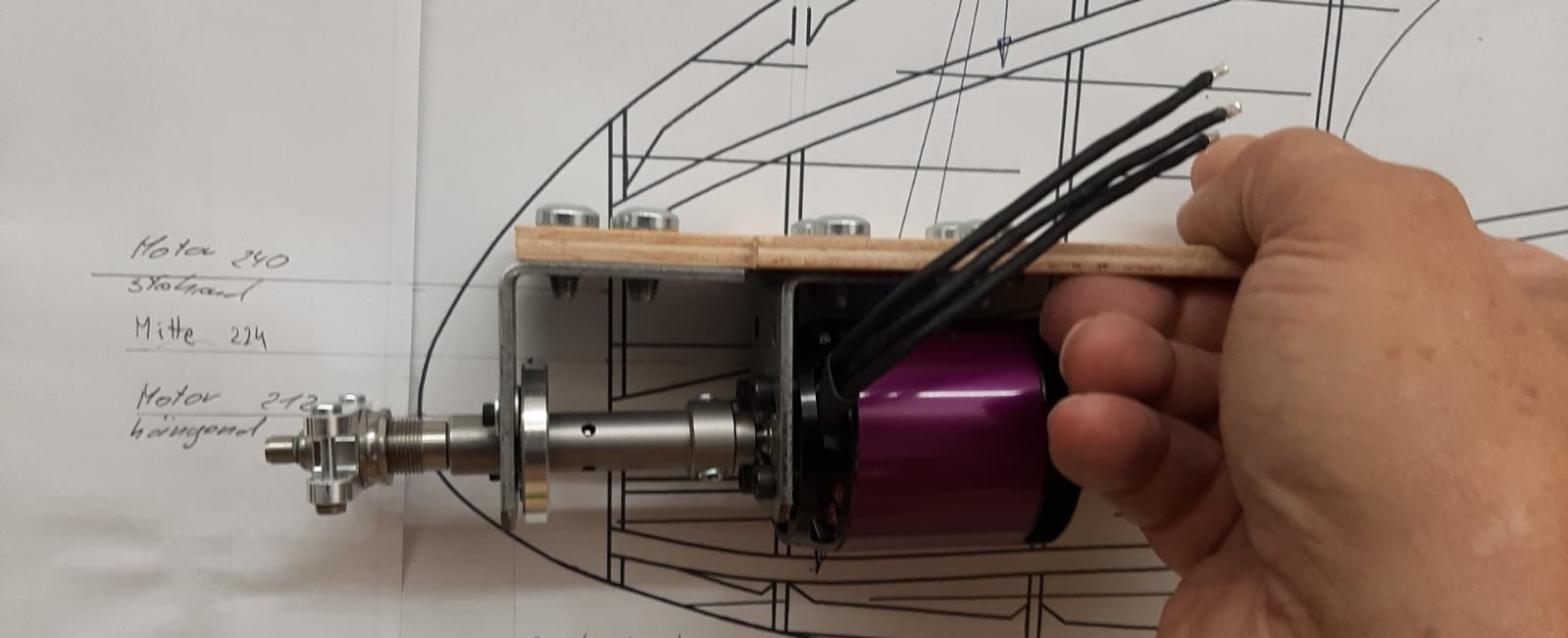
„Anprobe“
Das Kürzen der Trägerplatte zeigte schon eine Verbesserung.

Trägerplatte gekürzt
Um auch den Lagerspant nach hinten zu versetzen, habe ich das Lager außen montiert und den Winkel gekürzt.

Lagerspant modifiziert
Jetzt konnte ich den Durchbruch im Rumpfspant ausschneiden und einen ersten Probeeinbau durchführen.

Probeeinbau
Die Trägerplatte habe ich auf einen Holzblock montiert, der an der Oberseite eine Schräge von 2° erhielt.
Dadurch wird der Motor um 2° nach vorne geneigt.
Den Block habe ich mit 6 mm Sperrholz verkleidet und seitlich die beiden Akkus für die Servos montiert.
(von diesen Zwischenschritten habe ich leider keine Fotos)
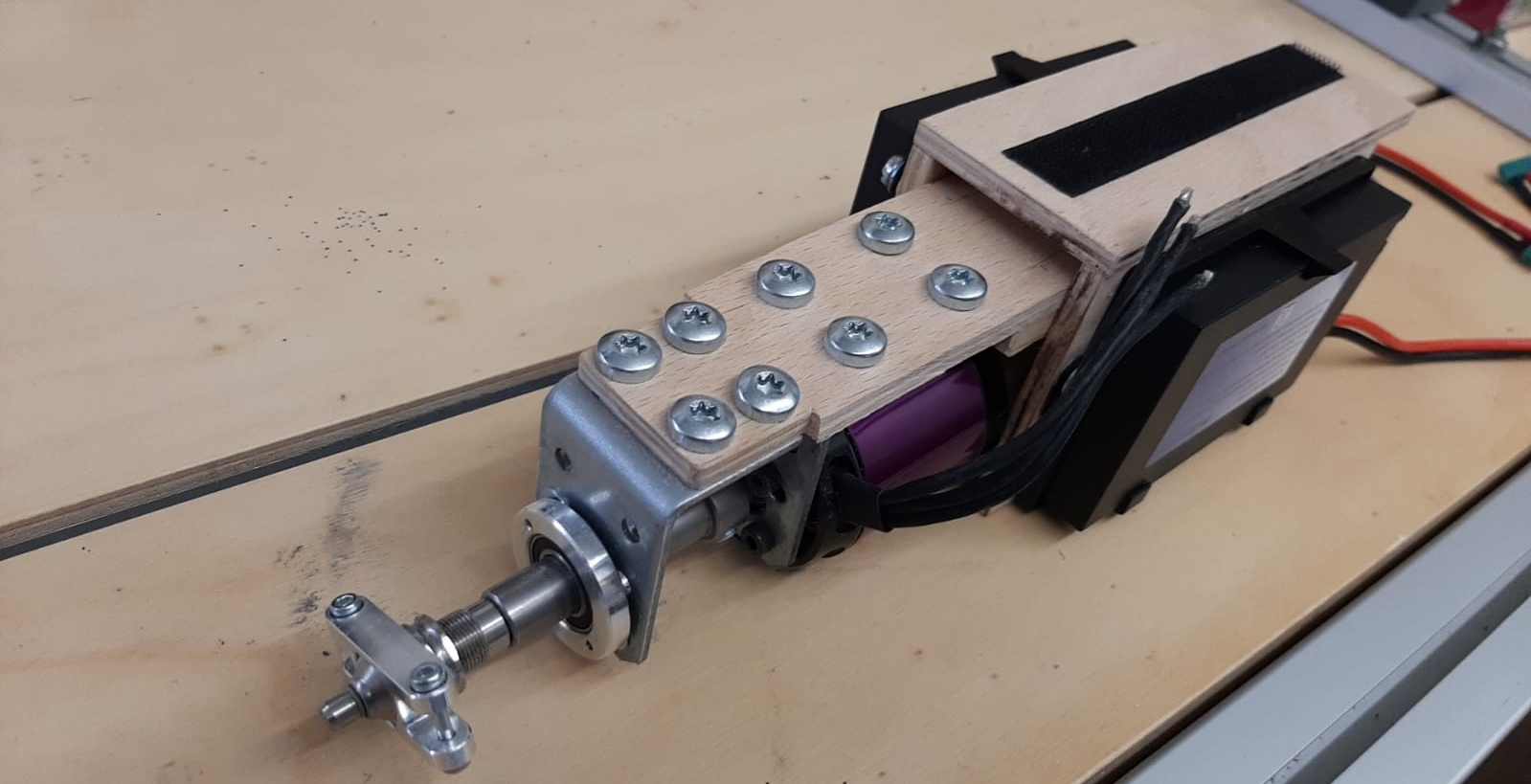
Antriebseinheit mit Servoakkus
In der Ansicht von unten kann man den Holzblock erkennen

Antriebseinheit mit Servoakkus
Das Klettband auf der Oberseite ist für den Motorakku vorgesehen.

Akkumontage
Die Position des Reglers auf dem Akku ist noch nicht endgültig – er wird später vor dem Akku montiert.

Antriebseinheit komplett
Die vordere Position der Antriebseinheit erhält eine exakte Führung und gleichzeitig eine Verstärkung aus einer Siebdruckplatte mit einer Dicke von 16 mm. Die beiden Unterlegscheiben dienen als Anschlag.

Arretierung der Antriebseinheit
Zur Befestigung der Antriebseinheit verschraube ich von unten einen Block, in dem eine Einschlagmutter M5 montiert ist, auf der Kufe.

Befestigungsblock
Die Antriebseinheit erhält einen Befestigungswinkel an der Rückseite des Holzblocks

Befestigungswinkel
Die Position des Antriebsakkus rückt etwas nach hinten. Dadurch kann der Regler vor dem Akku platziert werden.

Montage des Antriebsakkus und des Reglers
Die Antriebseinheit verschraube ich mit dem Haltebock. Durch die Arretierung (Siebdruckplatte) an der Nasenspitze ist keine weitere Befestigung erforderlich.
Eine Entnahme der kompletten Einheit ist durch Lösen dieser einen Schraube einfach zu erledigen. Das Laden der Akkus außerhalb des Rumpfes ist dadurch schnell und komfortabel möglich.

Befestigung im Rumpf
Die beiden Langlöcher am Befestigungswinkel ermöglichen eine Feineinstellung der Motorneigung.

Einstellung der Motorneigung
Die Rotorblätter haben noch ca. 20 mm Platz zum Boden. Ein Probelauf des Motors vor dem Start ist damit noch möglich.

Probeeinbau Rotorblätter

Probeeinbau Rotorblätter
Die komplette Antriebseinheit bringt ca. 2,2kg Gewicht in die Nasenspitze. Dadurch wird das zusätzliche Ausgleichsgewicht zum Einstellen des Schwerpunktes minimal ausfallen.

Gewicht der Antriebseinheit bisher: 2216g
In der Zwischenzeit beginne ich mit dem Aufbau der Nase und baue parallel dazu außerhalb des Rumpfes an der Antriebseinheit weiter.
Die Beschreibung der Nase folgt weiter unten, damit der Bericht nicht zu verwirrend wird.
In meinem Kleinteile-Fundus habe ich zwei Federblech-Halterungen gefunden, die perfekt zur Befestigung der Motorsteuerung geeignet sind.
Ursprünglich waren es Klammern eines rahmenlosen Bildhalters.
Diese beiden Klammern schraube ich an der oberen Trägerplatte an.

Federblech-Halterungen
Durch einfaches Einclipsen in den Kühlrippen arretiert sich die Steuerung von selbst.

Steuerung von hinten
Die Kühlrippen zeigen dabei in Flugrichtung und werden optimal gekühlt.
Da der Motor lediglich als Starthilfe und als Sicherheit dient, wird eine kurzzeitige Laufzeit keine sonderlich hohen Temperaturen erzeugen und die Gefahr einer Überhitzung ist damit äußerst gering.

Steuerung von vorne
Ebenfalls aus dem Fundus stammen die beiden Winkel zur Aufnahme des Motorakkus.

Aufnahme Motorakku
Mit Schrauben aus dem Möbelbau werden die Winkel am Träger der Antriebseinheit verschraubt.

Winkelbefestigung
Die Schraubenköpfe dieser Schrauben sind nahezu bündig mit der Auflagefläche des Akkus.

Winkelbefestigung
Durch das Klettband zur Sicherung des Akkus gegen ein Verschieben wird der Überstand der Schraubenköpfe ausgeglichen und der Akku kommt nicht mit ihnen in Kontakt.
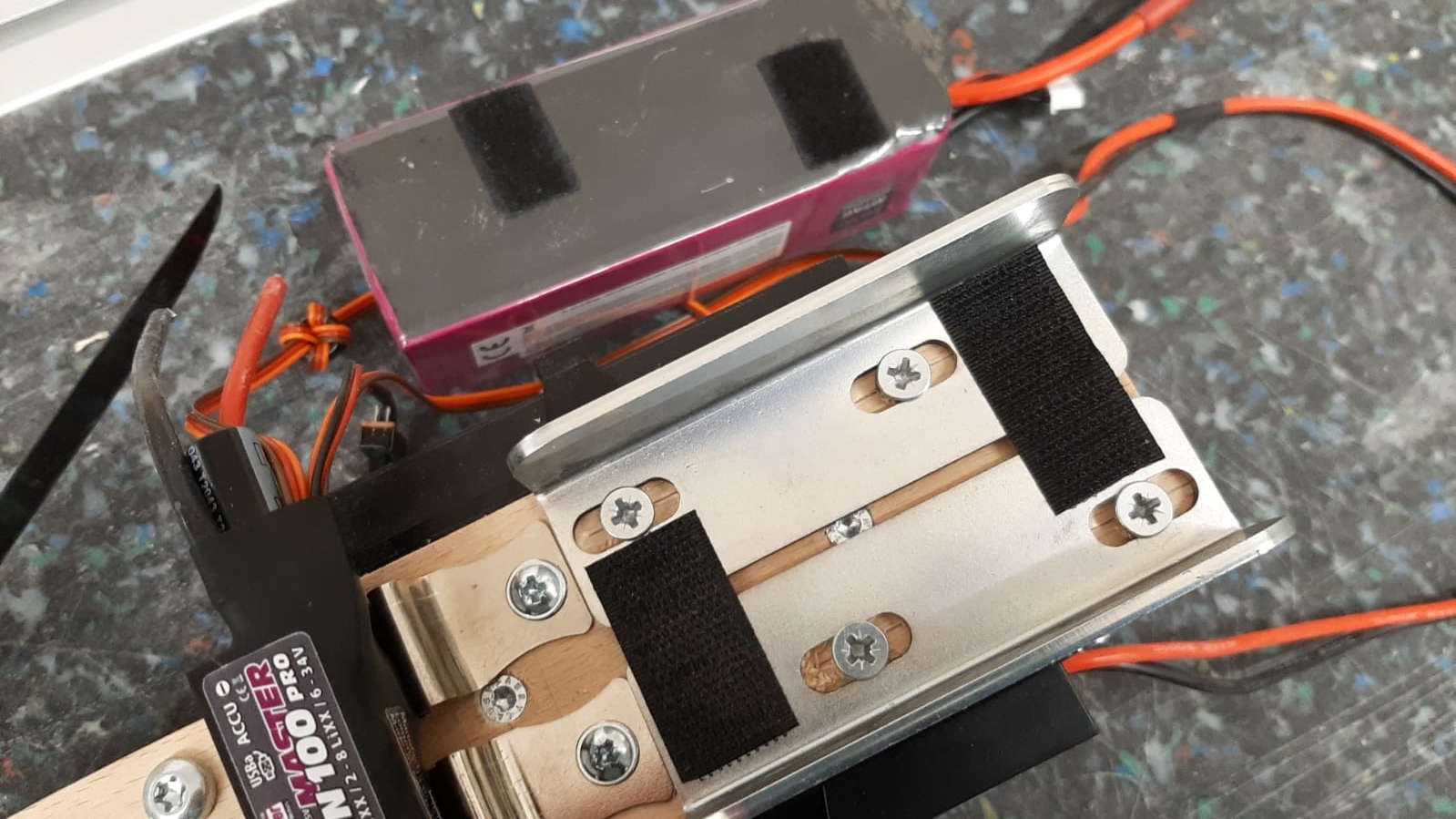
Klettbandsicherung
Die beiden Federbleche der Steuerungshalterung wirken dabei als Anschlag für den Akku und verhindern einen Kontakt des Akkus mit der Steuerung. Dadurch wird eine Wärmeübertragung weitgehend unterbunden.

Anschlag
Den Akku habe ich dann noch um 180° gedreht um die Kabel des Akkus so nah, wie möglich an die Motorsteuerung zu bringen.
Ein Verlängern der Kabel ist somit nicht erforderlich.
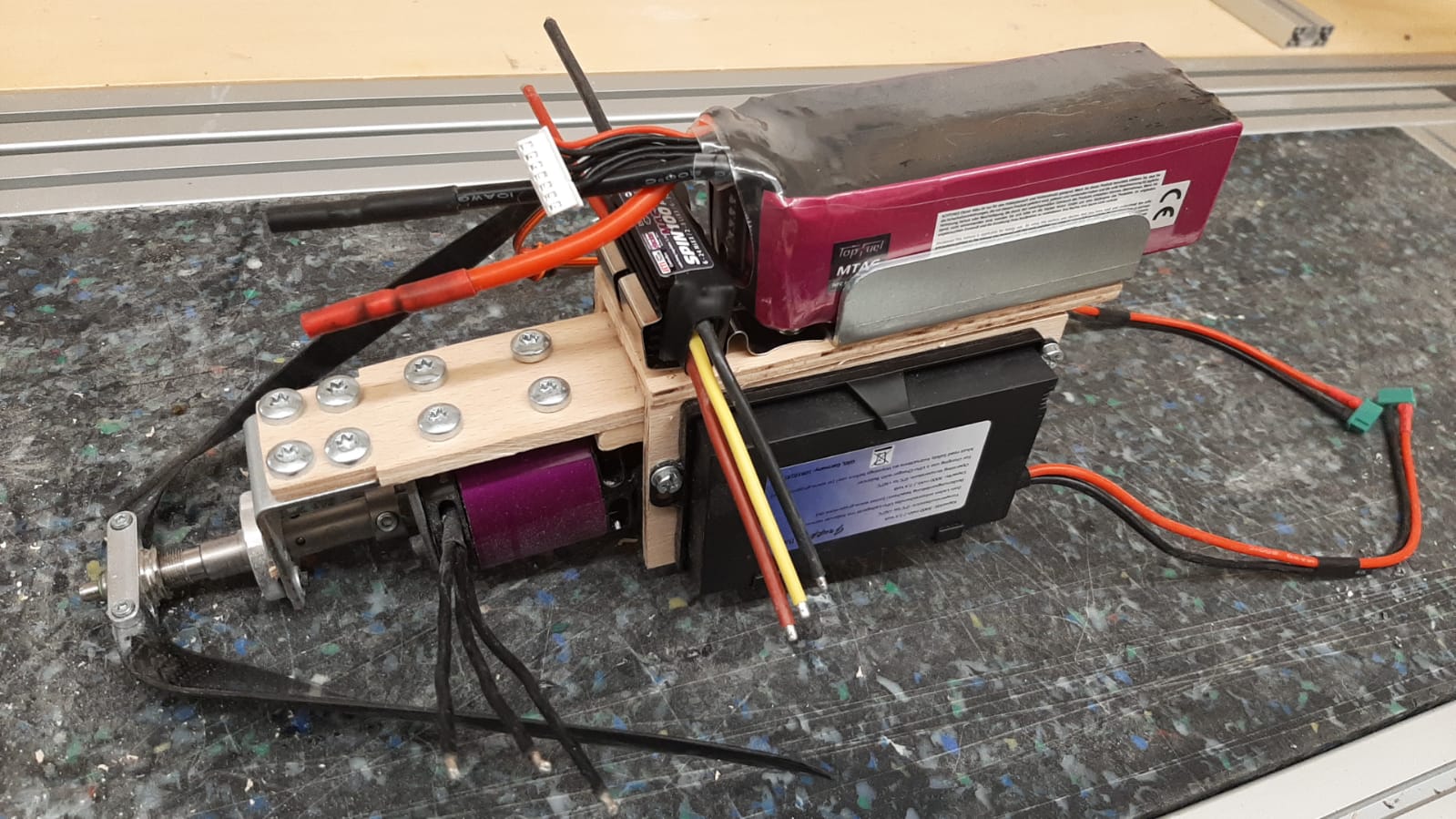
Übersicht Antriebseinheit
Ein Probeeinbau zur Kontrolle zeigt keine Probleme – ich kann also mit der Verkabelung und den Lötarbeiten beginnen.

Probeeinbau
An die Kabel des Reglers und des Motors werden Goldstecker und Kupplungen angelötet und mit Schrumpfschlauch isoliert.
Ich fixiere die Kabel mit einer kleinen Nagelschelle an der Trägerplatte des Motors.

Kabelverbindung Motor/Regler
Die Stromzufuhr wird ebenfalls mit Goldsteckern verlötet und isoliert.

Kabelverbindung Regler/Akku
Für den Schalter des Reglers schneide ich ein Buchenholzbrett zurecht und befestige es seitlich am Träger.
Die Kabel zum Empfänger fixiere ich ebenfalls mit einer Nagelschelle.

Schalter und Kabelbefestigung
Mittlerweile hat die gesamte Antriebseinheit ein Gewicht von 2,45 kg.
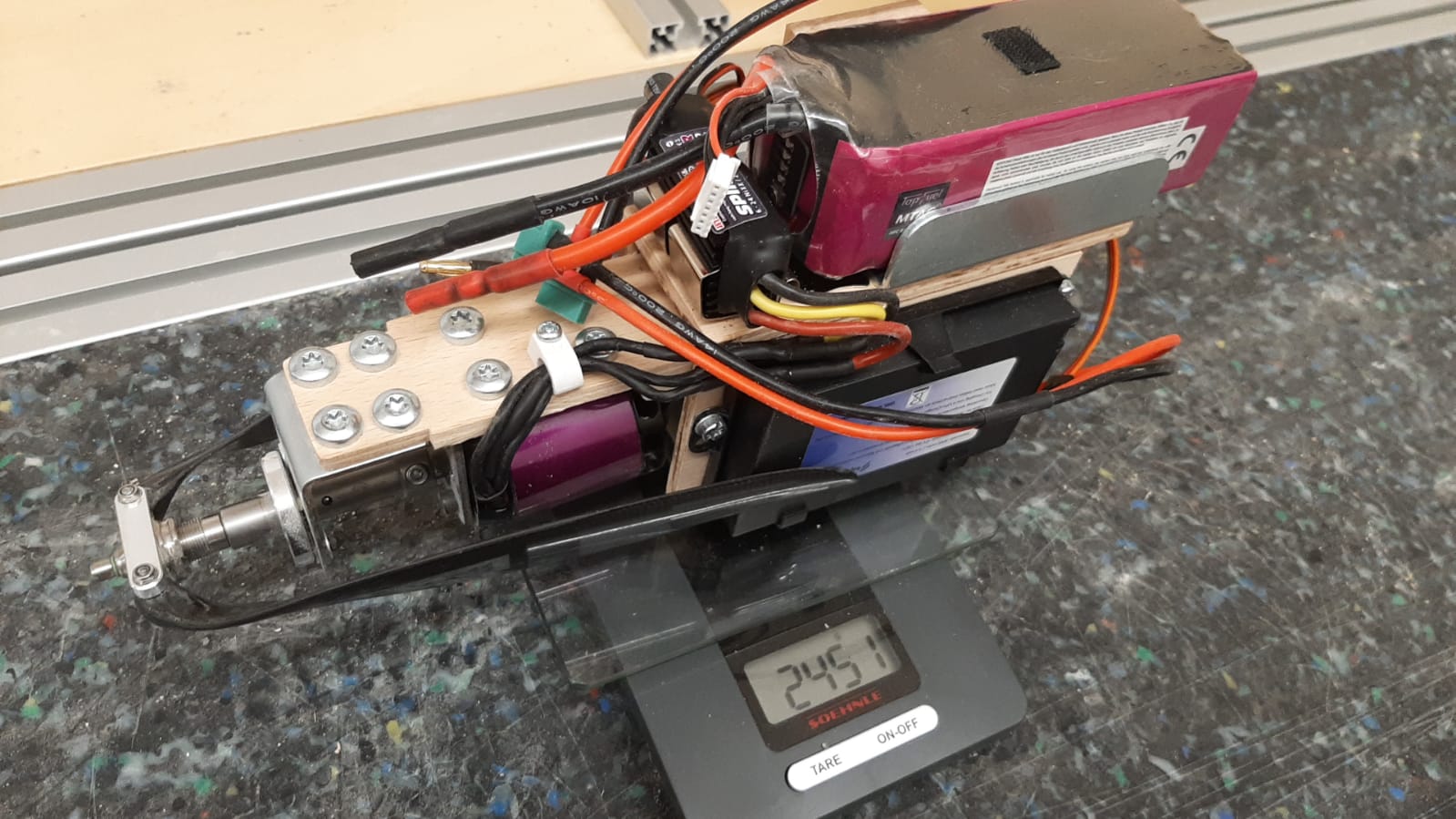
Antriebseinheit 2,45 kg Gesamtgewicht
Der Probeeinbau lässt sich problemlos durchführen – der Schalter ist gut erreichbar – alle Kabel haben genügend Platz und werden nicht geknickt oder geklemmt.
Das Gestänge der Schleppkupplung ist freigängig und hat keinen Kontakt zur Antriebseinheit oder den Kabeln.

Probeeinbau
Der Rumpf ist inzwischen umgespannt. Ich habe einen Gewindestab durch das Vierkantrohr der Tragflächen-Steckung geschoben und kann damit den Schwerpunkt auswiegen.
Aktuell ist der Rumpf etwas kopflastig, was mir genügend Spielraum beim weiteren Aufbau lässt.

Schwerpunktwaage
Um eine grobe Schätzung zu erhalten, wie die Gewichtsverteilung aktuell ist, stelle ich die Waage unter die Front.
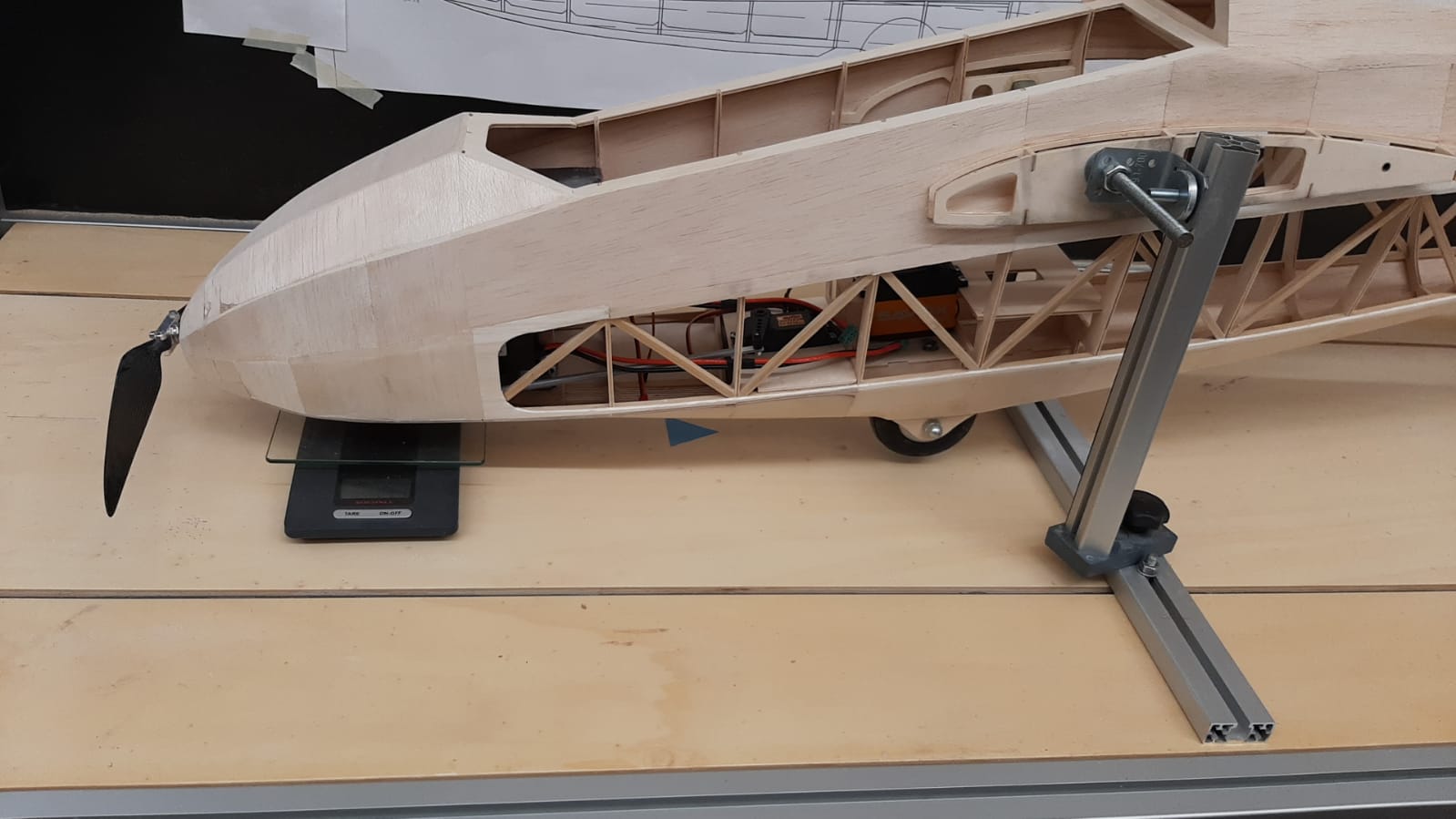
Ermittlung der Gewichtsdifferenz
Die Kopflastigkeit beträgt ca. 490 g – mal sehen, wie es sich weiter entwickelt…

Kopflastigkeit ca. 490 g
Fortsetzung folgt…
Die Nase:
Die Nase bilde ich aus einzelnen Balsaholzblöcken (10-15 mm dick) und Brettchen (1-3 mm dick), die ich als einzelne Segmente um die Motorführung herum ansetze.

Nase segmentweise angesetzt
Diese werden nun grob vorgeschliffen.

Vorschliff der Nase

Balsaholzblöcke, 2. Lage

grober Zuschnitt der 2. Lage

grober Schliff der 2. Lage
In das Abschlussbrett bohre ich ein 8 mm Loch und richte die Platte mit Hilfe eines 8 mm Bohrers an der Propellerachse aus.

Abschlussplatte
Die Nasenspitze schleife ich grob vor.
Hierbei achte ich auf eine möglichst symmetrische Form.

Grobschliff der Nasenspitze
Schon hier versuche ich die Kantenverläufe alle auf die Mitte der Propellerachse auszurichten.
Beim späteren Feinschliff wird das Ganze noch verfeinert und die einzelnen Flächen bekommen dadurch einen harmonischen Gesamteindruck.
Ich werde auch den weiteren Kantenverlauf nach hinten beim Feinschliff symmetrisch anlegen.
Die noch vorhandenen kleinen Krümmungen und Knicke sind dann ebenfalls weitgehend verschwunden.

Kantenverlauf zur Propellerachse gerichtet
Mit einem Bohrer, den ich mit Schleifpapier beklebt habe, weite ich die Bohrung vorsichtig auf ca. 13 mm. Somit verhindere ich ein Einreisen des Holzes.
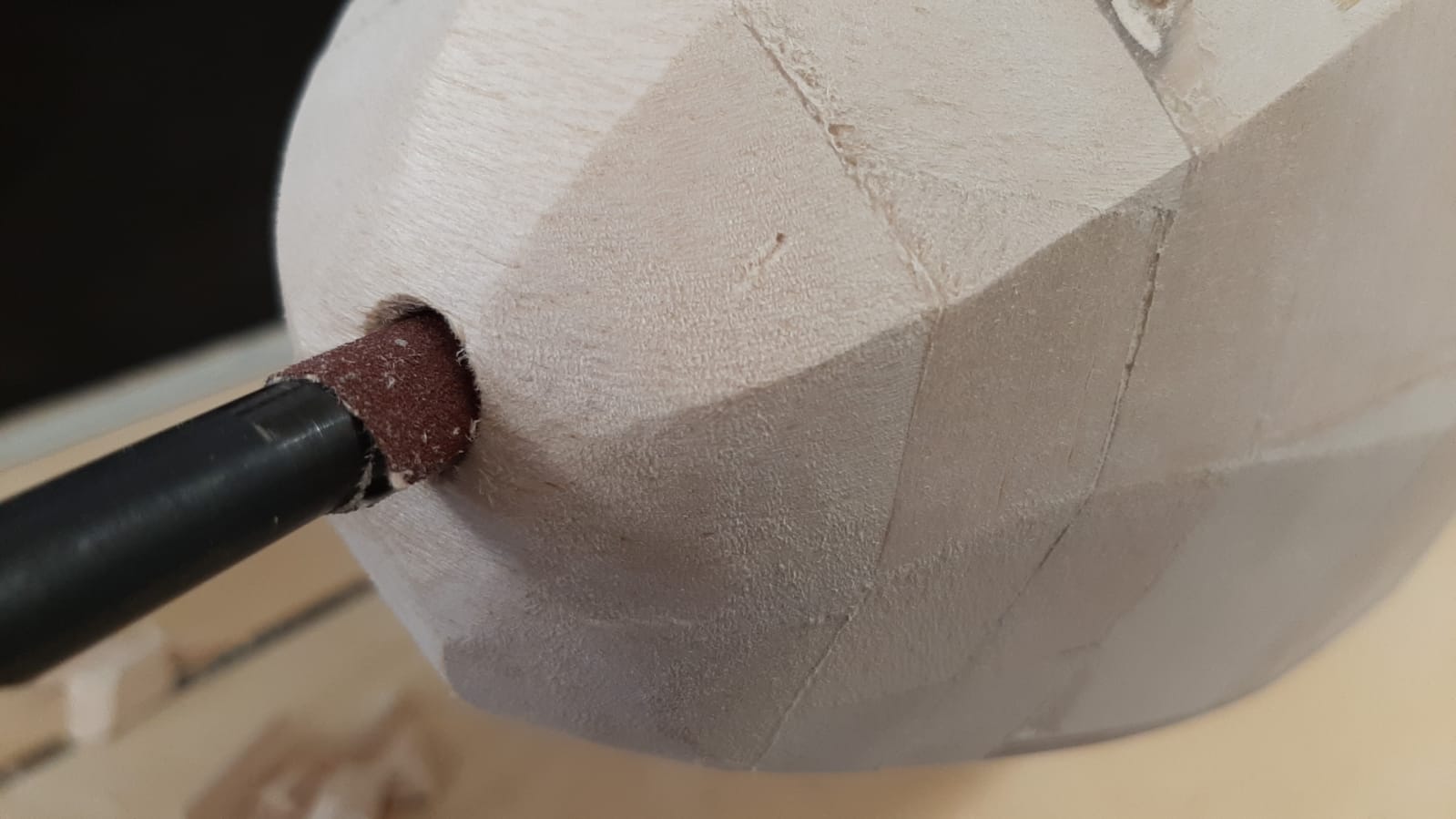
Ausschleifen der Spindelbohrung
Die Propellerspindel hat nun sowohl im Durchmesser, als auch im Abstand zur Nasenspitze ein wenig Luft und kann völlig frei rotieren.
Die 4 oberen Kanten habe ich zwischenzeitlich einem ersten Feinschliff unterzogen und habe damit die erforderliche Form nahezu erzielt.
Die unteren Kanten werden geschliffen, wenn ich den Rumpf umgespannt habe.

Einpassen der Propellerspindel
Die Kanten der Unterseite laufen nun auch alle auf die Spindelachse zu.
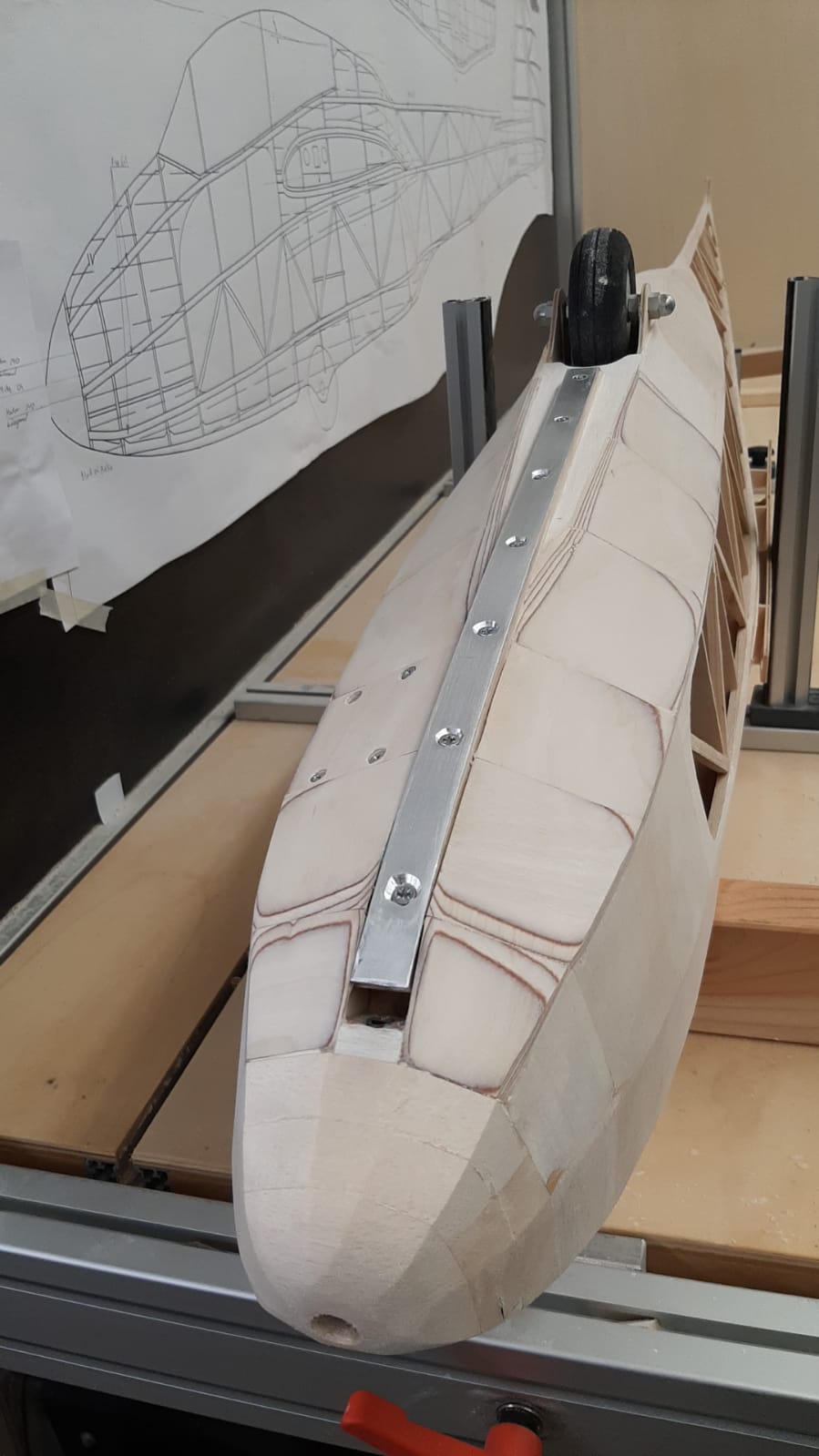
Nasenunterseite verschliffen
Fortsetzung folgt…